Let’s conduct a thought experiment: imagine a rubber tire and a steel tire in the same environment on the road. You apply the same amount of adequate force to roll each one. After some time, both stop moving. But if you measure the distance both covered, which one would travel further?
As the engine runs, the linear motion of pistons is converted into circular motion to roll the wheels, allowing the car to move. While driving, tires are exposed to external force, causing the tire to deform due to the weight of the automobile. As the tires rotate, they constantly deform and recover. As a result, the material of the tire, which is the rubber, stretches. During compression and recovery of the tire, there is always energy transfer between these two processes. However, not all energy is recovered fully; some is converted into heat, known as Hysteresis, causing rolling resistance. So, the tire enters a cycle, continuously undergoing compression and expansion. Therefore, it goes through the Hysteresis Cycle, resulting in energy loss. Due to this energy loss, rolling resistance occurs. The more a tire deforms, the more a car encounters rolling resistance. This means the engine needs to run a bit harder to maintain a constant velocity, causing it to consume more fuel.
Now let’s take a closer look at why this energy loss occurs. A perfectly elastic material would be one that returns to its original size without any energy loss after being deformed, regardless of the force applied. Unfortunately, such materials do not exist in the real world, because some energy is always converted into other forms like heat due to molecular interactions and internal friction.
In an ideal scenario with a perfectly elastic tire, the contact point with the ground would be a single line. However, in reality, tires have a contact area with the ground, known as the patch area. This contact area forms because the tire is deforming constantly while rolling. This is what again leads to hysteresis and energy loss.
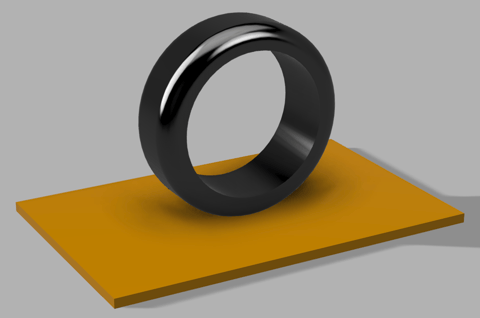
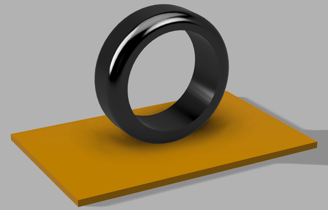
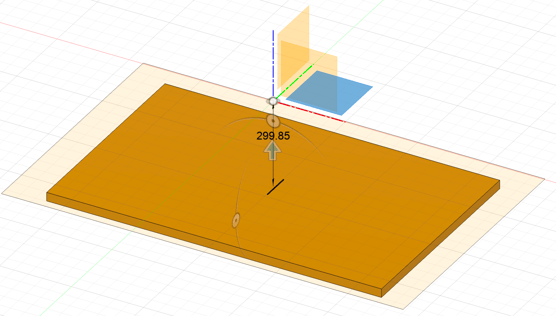
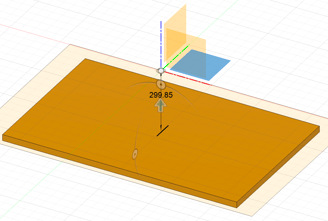
A Tire In Contact With The Road
Line of contact between a perfectly elastic tire and the road
Returning to our thought experiment, the rubber tire travels a shorter distance than the steel tire because rubber is not as perfectly elastic as steel. Instead, rubber is viscoelastic, meaning it consists of long-tangled polymer chains exhibiting a viscous effect, leading to energy loss during deformation and recovery. That is why a rubber tire slows down and eventually stops on its own after some time: it has lost the kinetic energy that was moving it forward, since the energy has been dissipated as heat.
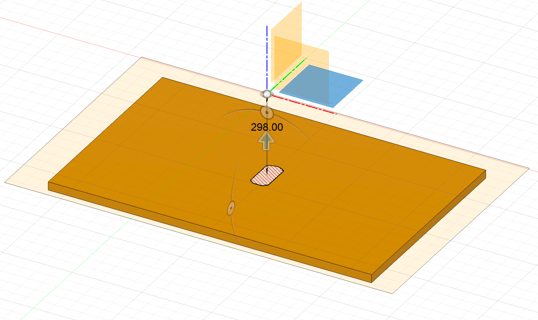
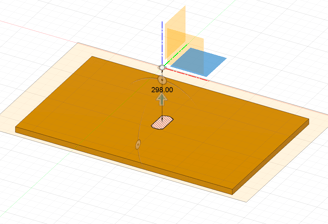
The patch area formed between a normal tire and the road
In contrast, steel does not exhibit significant viscoelastic effects, which is why it experiences much less rolling resistance. This is why a rubber tire travels less distance than a steel tire.
There are ways to reduce rolling resistance, listed below.
Softer materials increase rolling resistance because they deform more. Harder materials deform less but compromise ride comfort.
Lower tire pressure enlarges rolling resistance. Since the tire surface increases, it deforms more.
As the weight of the vehicle increases, larger rolling resistance happens due to again the enlarged contact area between the tires and the road.
Because of these factors, engineers conduct as many experiments as they can to determine the best material, pressure, and weight of automobiles to have an optimum driving experience.
ROLLING RESISTANCE
Did you know that up to 20% of a gallon of fuel consumed by an average automobile is used to overcome rolling resistance? In electric cars, rolling resistance can reduce 15% of the vehicle’s total range. Can you imagine the potential savings if rolling resistance could be minimized? This article covers the logic of rolling resistance and will help you to understand why it happens.
In the end, a significant amount of fuel is consumed to overcome rolling resistance, and this quantity of fuel can extend the total range a car can achieve. Hence, minimizing rolling resistance is important. Since rubber is not a perfectly elastic material and shows viscoelastic behaviors, during the tire's compression and expansion, it results in heat – a phenomenon known as Hysteresis- leading to energy loss. Consequently, engineers are continuously seeking the optimal design parameters such as tire pressure and wheel hardness that mitigate this loss without compromising driving comfort. As technology evolves day by day, improved tire design will provide higher energy efficiency and a better driving experience.
Eren Erden
Get in Touch
02erenerden@gmail.com