Dye Penetrant Inspection (DPI)
Dye penetrant inspection (DPI), also referred to as liquid penetrant inspection (LPI), is a non-destructive testing method to locate surface flaws such as cracks, laps, and porosities on the product.
These discontinuous on the surface are mainly caused by machining operations like casting, forging, and welding. The applicability of this method is not only limited to metals but is also valid for non-porous materials, including glasses, plastics, and ceramics.
Detecting defects is crucial in the aerospace, automotive, and power generation industries.
What makes this technique unique is its portability, which can be applied everywhere. Hence, both engineers and technicians use this technique in such industries.
Let’s clarify the steps one by one.
The surface of the product is cleaned and ensured that there are no dirt and dust particles on the surface.
Enough time is given to penetrant to soak into the invisible cracks.
The penetrant is applied.
The penetrant is inside the crack; it is not likely possible to clean it all out, no matter how much you try.
A special lubricant, known as developer, is applied. This is a must in dye penetrant testing because it locates the source of surface discontinuities by absorbing the trapped penetrant from the cracks and laps. As a result, it makes the source visible on the surface.
Afterward, the penetrant is cleaned by washing the surface.
Penetration time depends on the type of penetrant, but in most cases, the time required to soak into these cracks takes between five to thirty minutes. Required time also changes with the size of the cracks.
By following these steps, engineers and technicians can ensure the integrity, accuracy, and reliability of their products surfaces. Nevertheless, this method cannot detect the subsurface flaws. It is essential to complement it with other inspection methods when necessary.
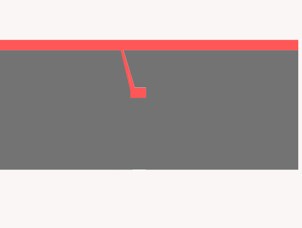
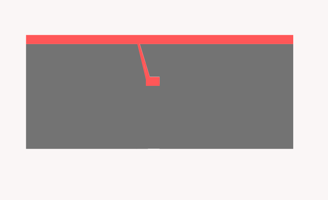
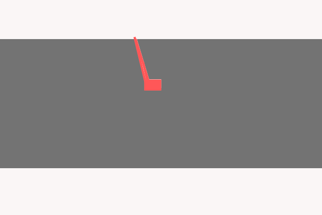
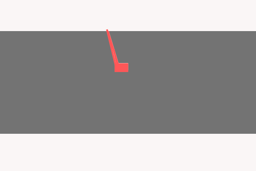
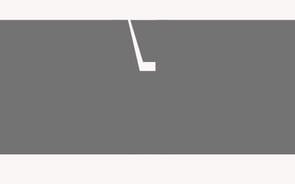
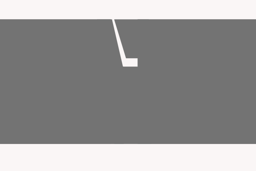
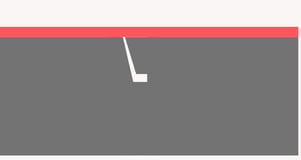
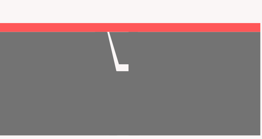
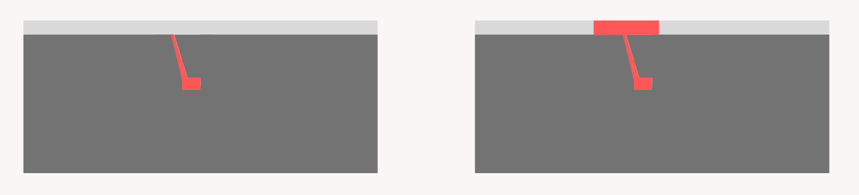
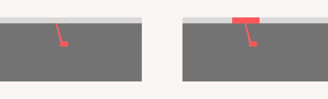
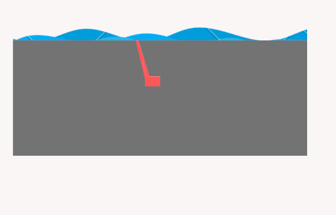
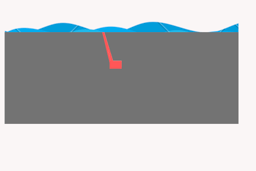
Eren Erden
Get in Touch
02erenerden@gmail.com