DNMG vs TNMG Turning Inserts
DNMG and TNMG are turning inserts or, in other words, cutting tools specifically designed for turning operations. They are used in the form of lathe machines, such as CNC turning centers, manual lathes, and multi-spindle machines. Which one would be used is determined in accordance with the customer’s requirements for the product.
When we examine the DNMG insert, it features a parallelogram-like shape with four cutting edges, two on the top and two on the bottom. It has an angle of 55 degrees on the corners, while TNMG is 60 degrees. TNMG is triangular-like in shape, containing six cutting edges, three on the upper edges and three on the lower edges.
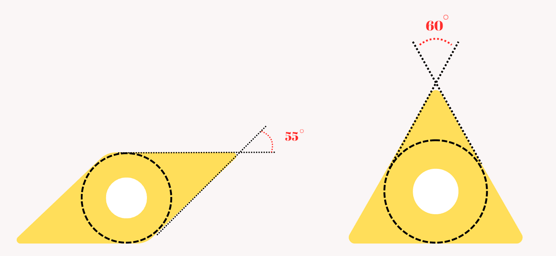
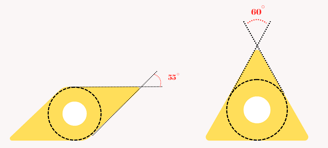
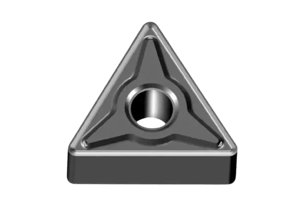
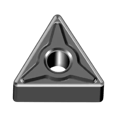
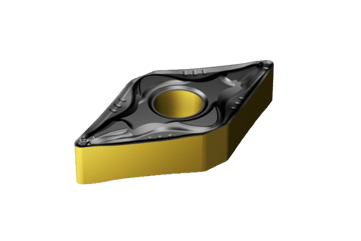
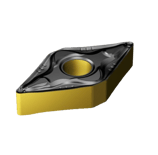
To specify the differences of each cutting tool, we must separate the type of work in two ways: precision and roughing.
If your job requires taking as much material as possible, TNMG is a better choice. In addition, six edges on the corners make it cost-effective for mass-production machining. Whereas DNMG insert is mostly utilized in the cases where precision is needed.
TNMG inserts are more durable in heavy-duty operations, on the other hand, DNMG inserts meet higher precision, versatility, and balance between finishing and roughing.
To give an example, DNMG inserts are preferred in softer metals like aluminum, brass, or stainless steel where smooth finishes are significant, while TNMG inserts handle tougher materials like cast iron, and high-carbon steels.
Now, let’s see some of the real-life examples.
The crankshaft of the engine is a crucial component of the engine, made from forged steel or high-carbon steel. This part of the vehicle is hard to be machined, requiring a high amount of force. Due to the high material removal rates and the durability of TNMG, the engineers typically prefer them for such applications.
To summarize briefly, both DNMG and TNMG are a must for turning operations in lathe machines for the applications of roughing, facing, profiling, and finishing. DNMG stands out with its performance in medium to light-cutting on metals like aluminum, brass, copper, and some soft steels. In contrast, TNMG specializes in high-feed and heavy-duty operations for harder materials. Steel, stainless steel, cast iron, and high-strength alloys are some of the examples. At the end of the day, the choice between DNMG and TNMG is determined by the material of the product and machining requirements.
Eren Erden
The Geometry of DNMG and TNMG
DNMG Insert
TNMG Insert
Get in Touch
02erenerden@gmail.com